PRODUCTS & SERVICES
Social Housing
At Ty Eco, we believe that ‘High Quality Housing’ isn’t about high cost—it’s about delivering outstanding thermal performance, acoustic comfort, and excellent air quality. Passive House (Passivhaus) standards ensure all of these, while also eliminating the performance gap between design and construction.
Councils and Housing Associations across the UK are increasingly demanding social housing that meets the Passive House Standard, and Ty Eco’s Adra PØ Building System is designed to make this achievable. By driving down the cost of building to this standard, we’re helping to make high-performance housing accessible to all and play our part in eliminating fuel poverty in the UK.
Adra PØ
Tŷ Eco’s Next Generation Timber Frame Building System for Passive House or Equivalent
MMC Panelised Passive ‘Eco’ House Building System

Next Generation Timber Frame Construction

Fully Sustainable Supply Chain

Drive down cost of building to PH Standard

‘Fabric First’ Approach

No Petro Chemical (PIR, EPS, XPS etc) Insulation

Local Supply Chain (for Carbon Footprint & Socio Economic Benefit)

Flat-pack’, Weather & Air tight Structure

Minimise use of Cement in Construction

Exceed all Building Regs. & LABC Warranty Standards for UK

Quick, Easy & Cost Effective to Build

Carbon Net Zero for Embodied Energy AND Whole life Carbon

Designed & Built in Wales
Panel Construction
Partel Exoperm Mono 150
11mm – 18mm Kronospan OSB3
300mm Masonite I Joists
Knauf Supafil Max Frame
12.5mm Medite Smartply ‘Airtight’
Partel Conexo Airtightness Tapes
Senco Fixings
Properties:
Precision Engineered utilising latest Technologies
Highly Robust & Easy to Assemble
Structural Airtightness of 0.6 ach or less
U Value of 0.12 W/m²K (before Internal & External Applications & Finishes)
Wufi Compliant (with Internal & External Finishes Calculated)
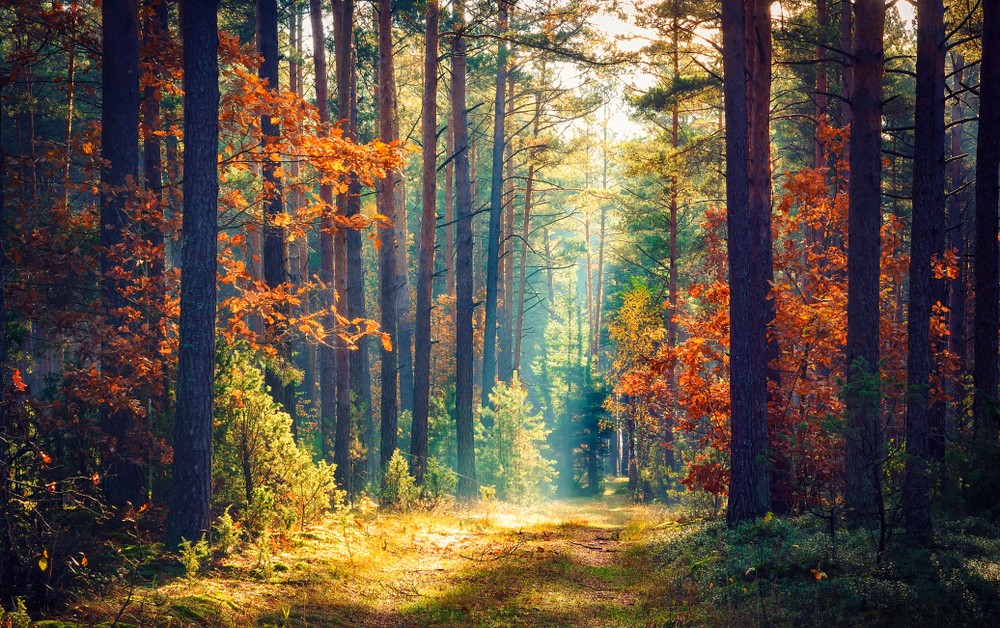
“OUR STATED GOAL IS TO DRIVE DOWN THE COST OF BUILDING PASSIVE HOUSE.”
On Time & On Budget
The reason many large housebuilders are moving away from traditional and building with timber frame is that it's fast and the costs more controllable. The same applies to any other building project, regardless of the size, quality or complexity.
With Timber Frame (particularly our Adra PØ system), you can go from slab to a complete structure that is weather tight, airtight and secure - ready for first fix - in a matter of days. Obviously some of this depends on the size of the structure and the specification you opt for - but you know how long it will take and how much it will cost well in advance.
Procurement Process
Early-stage Consultation & Advice
At Tŷ Eco we always encourage early-engagement on any project, but particularly with our Commercial and Social builders.
We strongly encourage early engagement for all projects, particularly with our commercial and social housing partners. We are more than happy to meet in person or via Teams to offer early-stage consultation and advice. A bit of guidance from us in the initial stages can save substantial time, reduce workload and ultimately, lower costs for everyone involved.
Whilst the Procurement Process is fundamentally the same as for smaller projects, for projects with multiple units, we are happy to bespoke the process to your needs and guide you through the process.
We aim to make our stage of the construction development as convenient as possible, ensuring your project is delivered on time & on budget - every time.
Let's get Technical
Good construction lives and dies on the quality of the technical & design details, get those wrong and it can result in hours of re-work or worse, a failure to meet the appropriate regulations. This is particularly true for the Passive House, BREEAM or AECB building standards.
All the information you need is on our Technical Resources pages, from our design details to the materials that they’re made from
Modern Methods of Construction
'M' isn't for Modular!
At Ty Eco, we believe Modern Methods of Construction (MMC) improve efficiency, sustainability and build quality by ensuring a factory-level finish, particularly for crucial elements like insulation.
Our panelised systems offer clear advantages over modular construction. Modular designs require transporting large, pre-built units (usually for long distances), often resulting in damage to finishes like plasterwork, brick, or render. Additionally, modular systems frequently use steel frames, which are inherently less thermally efficient and less sustainable than timber alternatives.
Centralised modular factories can de-skill local workforces and complicate addressing defects in the future. Ty Eco’s panelised systems avoid these issues, offering superior adaptability, quality, and sustainability.